We know how.
Become proficient in cleanroom floor jargon!
Our ABC glossary provides concise expert knowledge – so that you can be sure you are always in the know.
Anti-Bacterial Floor Coatings
According to studies, approximately 70 per cent of the bacteria in clean rooms enters via the flooring. To meet this challenge head on, anti-bacterial floor sealing can be an effective solution. The sealing has bacterio-static properties which prevent germs from proliferating: Due to contact with moisture, an environment is created that deprives germs of their natural living environment and severely hinders their reproduction. The floor coating can play a considerable role in improving hygiene in sensitive areas like clean rooms and lower the risk of contamination.
Leading innovators of cleanroom floors
in the pharmaceutical, automotive, and food processing industries
Certificates
Certificates confirm the quality and suitability of materials and processes which are particularly significant to comply with GMP guidelines. Especially in clean room coatings, certficates verify that the floors meet the strict demands with regard to emissions, particle control and chemical resistance. They guarantee that the coating does not contaminate, thus protecting the purity of the products. Without these certificates, companies risk violating GMP regulations. which can result in shutdowns or even the withdrawal of permissions. For this reason, certified materials and procedures are indispensable to guarantee the high quality and safety in GMP-compliant clean rooms.
Chemical Resistance
The chemical resistance of cleanroom materials is crucial due to their exposure to cleaning agents. Many aggressive chemical detergents, such as ethanol, hydrogen peroxide, or peracetic acid, are used in cleanrooms to ensure that all hygiene standards are met. Therefore, when choosing your cleanroom floor, it is crucial to select materials which are extremely chemical resistant and suitable for your specific cleaning requirements as the floor must be able to withstand repeated exposure to such chemicals without any adverse effects.
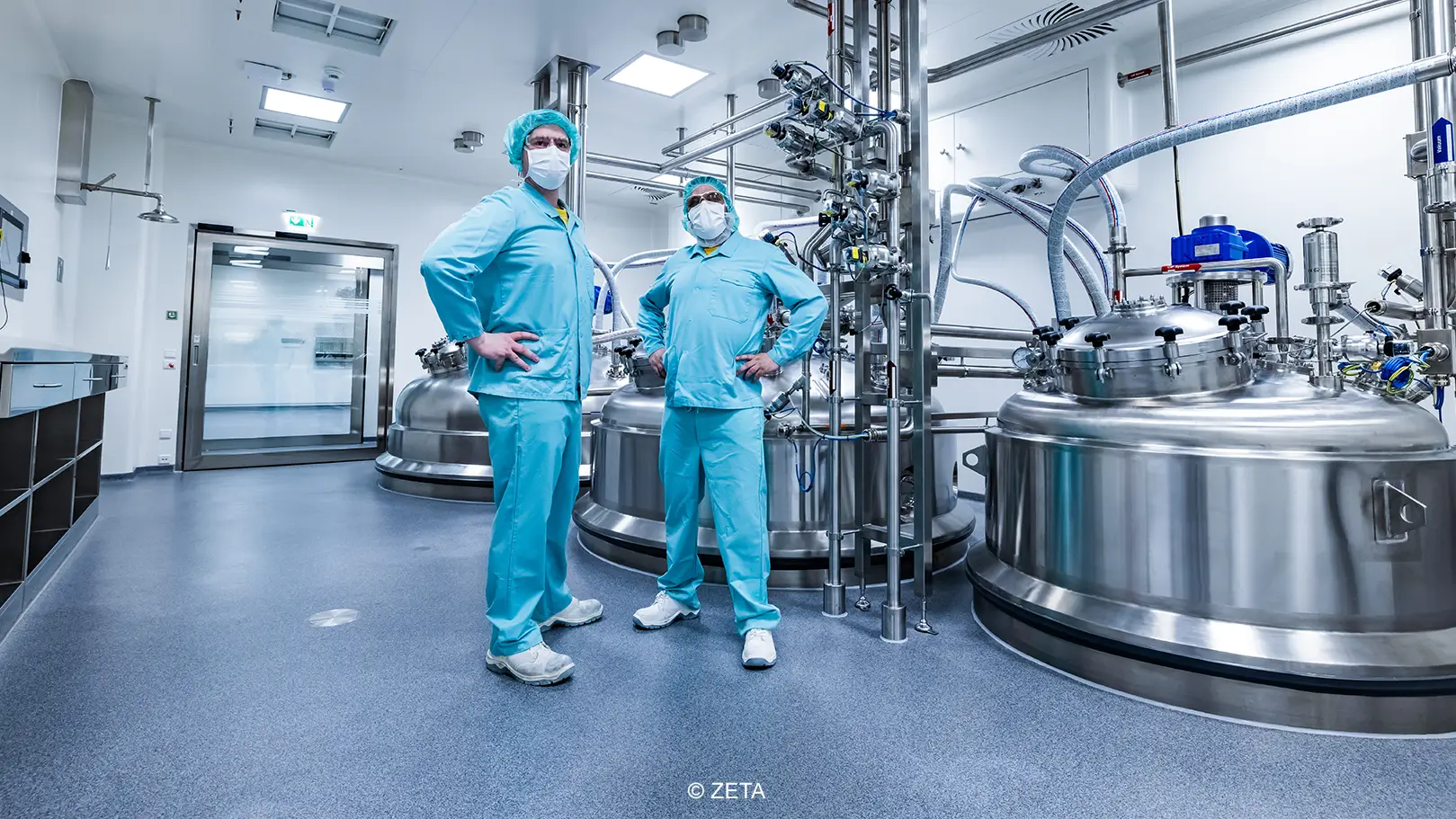
Cleanroom Floors
Cleanroom floors are special floor coatings which are applied in controlled environments, such as the pharmaceutical industry, laboratories, hospitals, and electronic manufacturing facilities. They are distinguished by their ability to effectively minimize dust, dirt, and other particles to guarantee a sterile and contamination-free environment. The floors are often seamless and manufactured using materials such as reactive resin, epoxy resin, or polyurethane since these are easy to clean and disinfect. In addition, they are resistant to chemical substances and provide high abrasion resistance. Cleanroom floors are an essential contribution towards meeting stringent hygiene requirements in sensitive areas.
Clean Room Classes GMP and ISO
Clean rooms are divided into various classes based on particle density although there are strict specifications on the maximum permissible level of particle concentration and size. This classification is based on the degree of air purity with stipulated limit values in standards such as DIN EN ISO 14644-1, VDI 2083, and the EG-GMP compass Annex 1. Regular particle measurements ensure compliance with the required cleanroom class. DIN EN ISO 14644-1 is mostly applied in chip manufacturing, microelectronics, optics manufacturing, and the automotive industry. The GNP compass (Good Manufacturing Practice) is particularly relevant in the pharmaceutical industry, biotechnology, and medical technology.
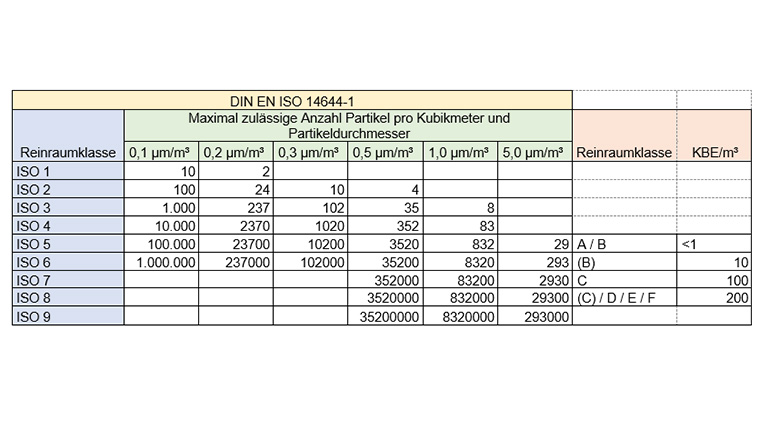
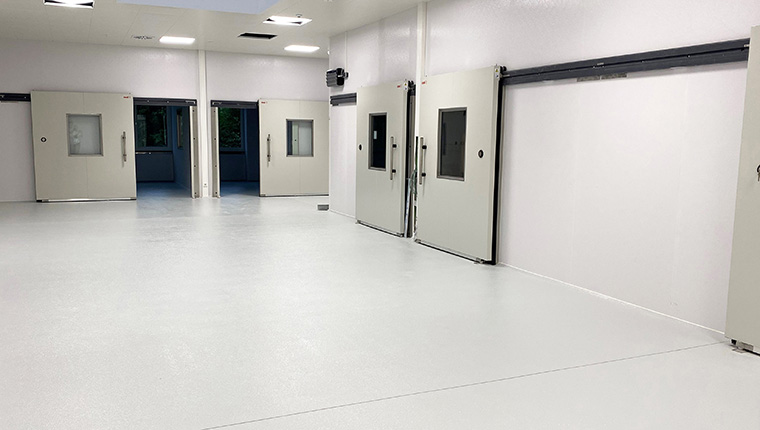
Coating
Floor coatings are special layers that are applied to floors to protect them from wear and tear, chemicals, and moisture. They often consist of epoxy resin, polyurethane, or acryl and protect as well as enhance the floor’s visual appeal. They are applied on industrial floors and in multi-storey car parks as well as in private homes. Depending on the requirements, they can come in slip-resistant, dust-free, and low maintenance designs. A high-quality floor coating not only prolongs floor longevity but also improves safety and hygiene in the rooms in which it is applied.
Cold Resistance
Epoxy resin is designed to provide a certain level of elasticity and absorb thermal movements without causing cracks or spalling. This flexibility makes epoxy resin robust and resistant in environments with moderate temperature fluctuations. Yet even these floors meet their limits when they are continuously subjected to extreme demands, for instance from liquid nitrogen. Since liquid nitrogen can reach temperatures of up to 196°C, a standard solution is insufficient. Instead, customized solutions are necessary which are tailored to meet the needs of the area of application.
Colour
The colour of a floor plays a key role in the total effect of the room. Not only does it influence the style and visual impact, but also the wellbeing of everybody in the room. Therefore, it is important to choose the right colour for show rooms, commercial rooms, production facilities, etc. Companies and industrial facilities are increasingly welcoming customers and visitors into their production halls. As a result, the purpose and function of these rooms is coming a more prominent aspect of their company and brand image. Colour-coordinated floors can enhance your corporate identity and create an attractive and professional ambience.
Concrete
Concrete often needs more than one coating to withstand environmental impacts, chemicals, and heavy-duty traffic. These coatings consist of epoxy resin, polyurethane, or acryl and offer added protection against moisture, cracks, and wear and tear. Particularly in industrial buildings and multi-storey car parks, these can prolong the longevity of concrete ceilings and floors and make them easier to clean at the same time. Furthermore, they can improve the aesthetic features of the concrete as they can help create smooth, coloured, or decorative surfaces. The important thing is that the coating is adhesive and tailored to meet the specific needs of the concrete and its use.
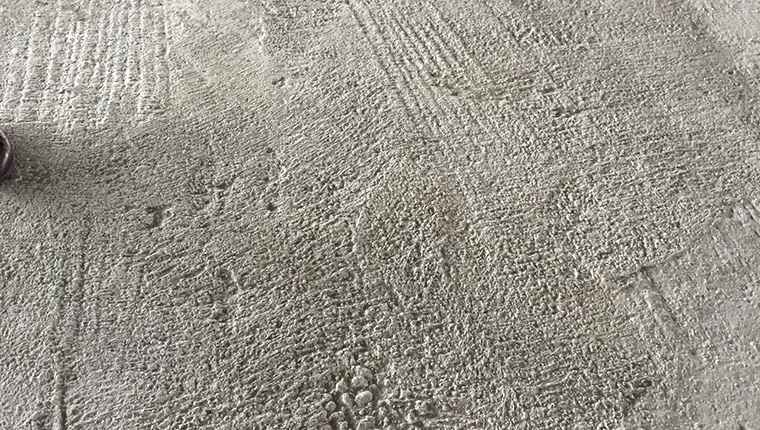
Conductive
Conductive floors are essential in clean rooms as they help to prevent potentially hazardous static discharge. Such discharges can be caused by friction or the separation of two materials and produce sudden discharges or sparks. In sensitive areas like clean rooms these can damage sensitive electronic appliances or even pose a fire risk. For this reason, conductive floor coatings are indispensable to guarantee safety and functionality in clean rooms. They reliably dissipate excess electrical charges, thereby reducing the risk of damage and accidents.
Cove Fillet
ABC always takes care to ensure that all cove fillets fit into the respective substrate. Fillets either have a rigid or floating design. We use special stainless steel profiles in the form of an L-angle or our own specially developed C-profile. The latter enables highly accurate floor edges and seamless transitions to walls. This technology allows the floor to move in unison with the substrate, preventing cracks, leaks, and the penetration of liquid. In this way, the integrity and function of the structure is protected. Sound planning and professional execution offer a safe and durable solution for sophisticated floor-wall connections.
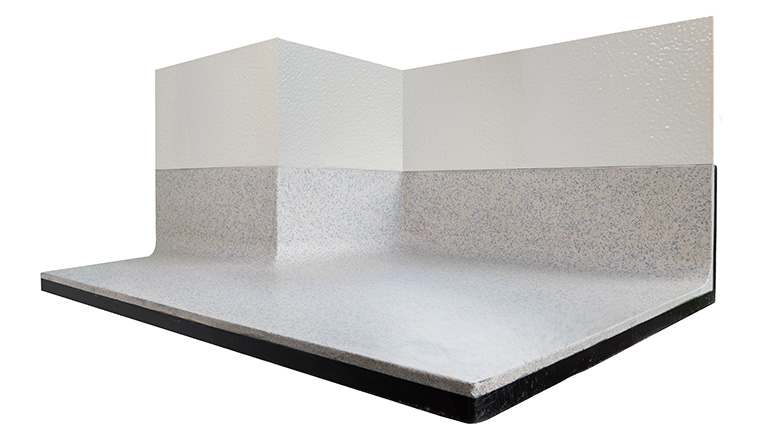
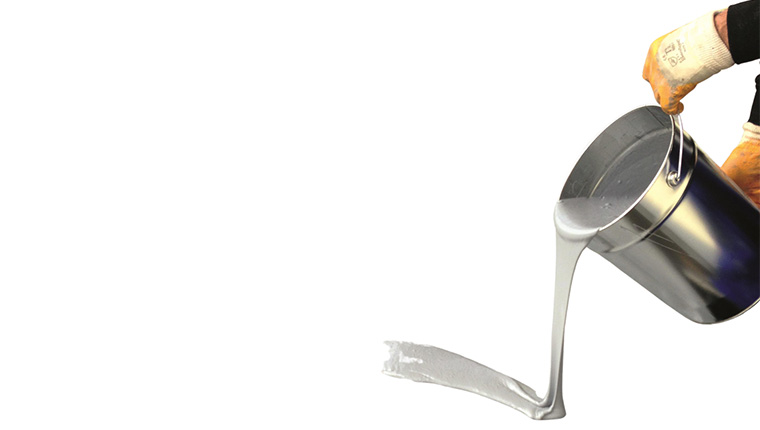
Epoxy Resin
Epoxy resin is artificial resin which is often used as coating as it is extremely robust, chemical resistant, and durable. It consists of two components – resin and a hardener – which are mixed together to form a robust and resistant layer after it has cured. Applying epoxy resin guarantees attractive floors that are seamless and easy to clean, making them a popular choice for industrial and commercial use as well as in private homes. Epoxy flooring is also resistant to chemicals, abrasion, and moisture so they are particularly suitable for use in challenging environments such as warehouses, garages, and cleanrooms facilities. The coating comes in a range of colours and surface structures to meet both functional as well as decorative needs.
Epoxy Resin Floor: Costs
The costs of having epoxy resin floors applied professionally in a commercial or industrial space are between €15 and €500/m². The exact price depends on many different factors: the condition and preparation of the substrate, the sealing, the chemical, thermal and mechanical requirements, the installation of drainage and concave fillets, working hours (e.g. night or weekend shifts), the standard-compliant design, cleanroom suitability, the desired certification as well as the warranty period and documentation. It is therefore difficult to quote a flat-rate price as the costs vary greatly depending on the project and the requirements.
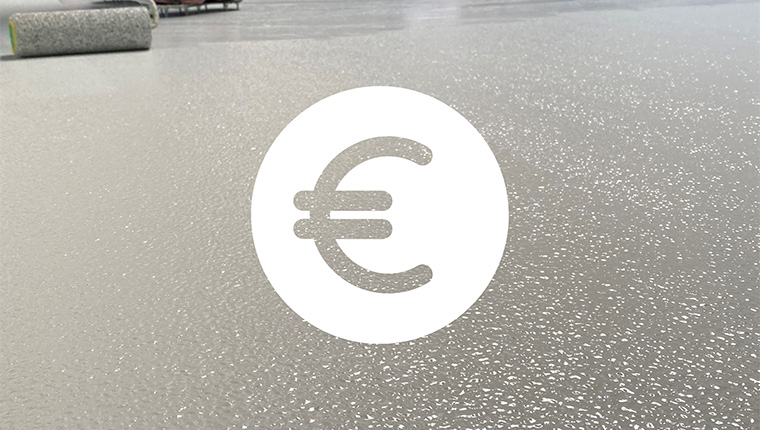
ESD
ESD stands for electrostatic discharge and requires special attention in clean rooms. Clean rooms are crucial for processes in which dust particles or other contaminants may impair the result. However, random ESD can damage sensitive components and compromise the reliability of the finished product. Therefore, it is essential to have extensive ESD protective measures in clean rooms. These include special floor coatings, clothing, and equipment to keep electrostatic discharge at a minimum and ensure safe grounding.
Excess Condensation
When applying coatings, condensation plays a keyrole as it marks the temperature at which air humidity begins to condense. Condensation which forms on the surface during application can impair adhesion and lead to severe problems like bubbles and delamination. To avoid this, it is essential to control both the surface and the air temperature as well as the relative air humidity. This can be done with the aid of hygrometers to ensure you have the right conditions to apply the coating. If these factors are not taken into account, it can lead to serious defects resulting in costly repairs.
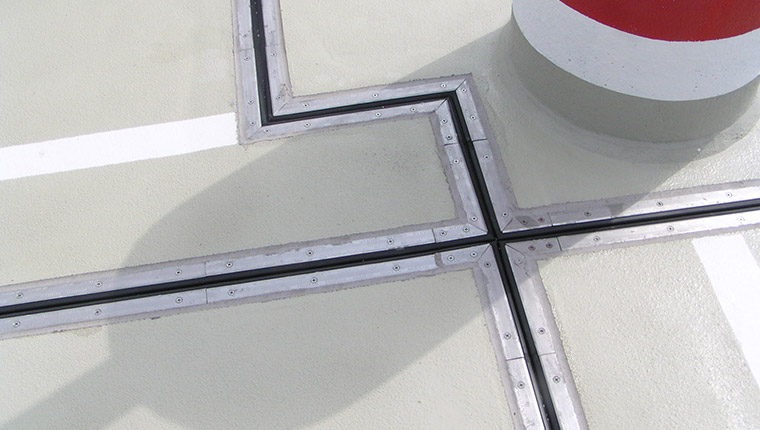
Expansion Joints
Expansion joints are specific joints in building structures which enable the building to expand and contract during changes in temperature or any other movements, without cracking. Particularly in large concrete expanses such as streets and bridges, these are crucial for releasing friction. The joints are often made of flexible material like rubber or silicon which can easily compensate a movement. Regular maintenance is necessary to ensure that they function properly and to prevent damage. Careful planning and professional installation of the joints are decisive to guarantee the integrity of the structure.
Flammability Classes for Floor Coatings
Our products are classified in accordance with EN 13501-1.
Non-combustible: A1fl
Flame-resistant: Bfl-s1, Cfl-s1
Normal flammability: A2fl-s2, Bfl-s2, Cfl-s2, Dfl-s2
Easily flammable: Efl, Ffl
The flammability class required depends on the respective national or country-specific regulations. As a rule, flammability class Efl is applied to private buildings while classes Cfl und Bfl are mostly required for commercial properties. In public buildings, especially in emergency stairwells and escape routes, materials classified as A1fl are mostly used in order to meet high safety standards.
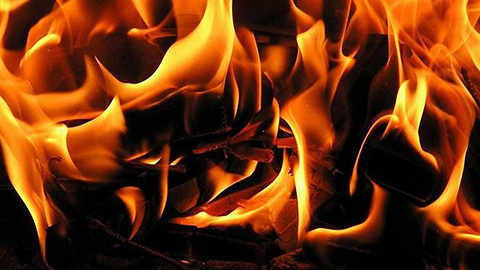
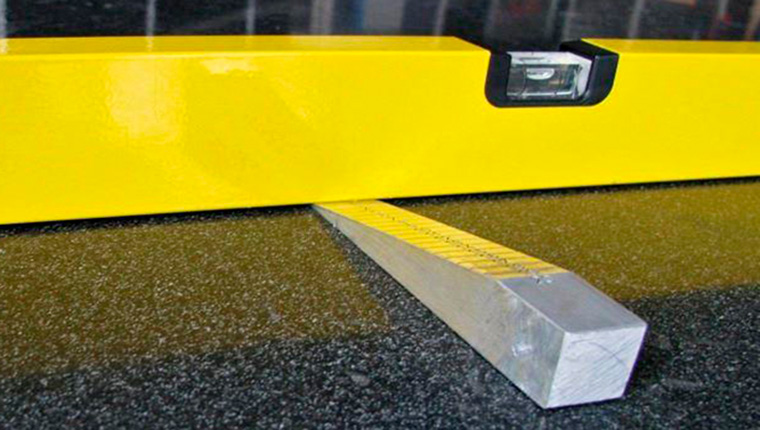
Flatness Tolerance
Flatness tolerance is a geometric term which applies to various areas like ceilings, subfloors, screed, floor layers, walls, wall panels, and suspended ceilings. The flatness of a surface is checked independently of dimensional and angle tolerances, usually with a spirit level and a suitable metal measuring wedge. To measure the flatness, the inside micrometer between two high points and the low point in between is measured, or vice versa. The distance between the dimensional points depends on the position of the high/low points. The important thing is that the spirit level is aligned neither vertically nor horizontally during the test. We recommend using a leveling Instrument for all large surfaces.
Floor Slope
The creation of slopes (or falls) in cleanrooms is often neglected during the planning process although water stagnation can cause severe damage to floors in these areas. To guarantee effective water drainage 2% slope towards the drains and channels is required. At the same time, it is important to take into account the purpose of the room. For example, can a heavy trolley roll freely if a slope is too steep? It is vital to find a balanced solution which provides for sufficient drainage on the one hand and safety and practicability on the other hand with regard to the specific production needs.
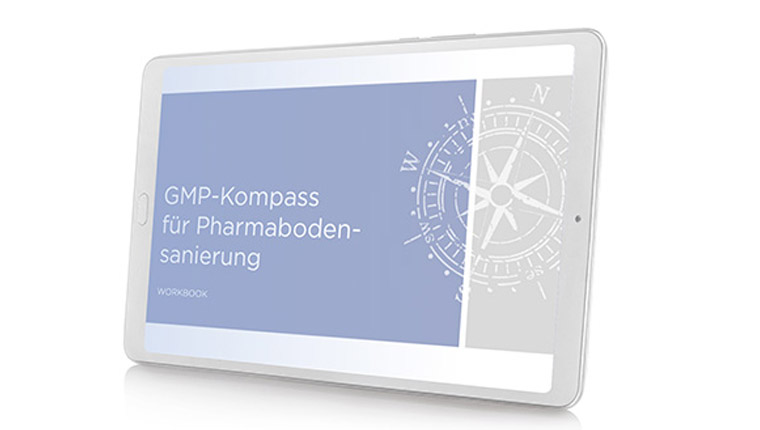
GMP
GMP (The Good Manufacturing Practice) defines the compliance of stringent quality standards during the production of medicaments, cosmetics, and food. These guidelines encompass all areas of production, starting with the raw materials to be used, the premises and equipment to staff training and hygiene. The main objective of GMP is to minimize the risks caused by contamination, inaccuracies, or mistakes during the production process. As a result, this serves to guarantee the safety and quality of the final product as well as protect consumer health. GMP plays a central role in ensuring that manufactured products meet the highest quality standards at all times. For more information, download our comprehensive GMP containing 160 guidelines.
Grinding
Grinding is an important process when preparing floor coatings as it ensures that the coating can bond properly to the substrate. The floor surface is smoothed with a grinding machine, the old coatings, uneven surfaces, and any dirt are removed. Grinding increases the floor porosity which improves the absorption of the new coating. This process ensures that the coating can be applied evenly and that it will remain durable. Grinding also reduces the risk of peeling or the formation of blisters in the new coating.
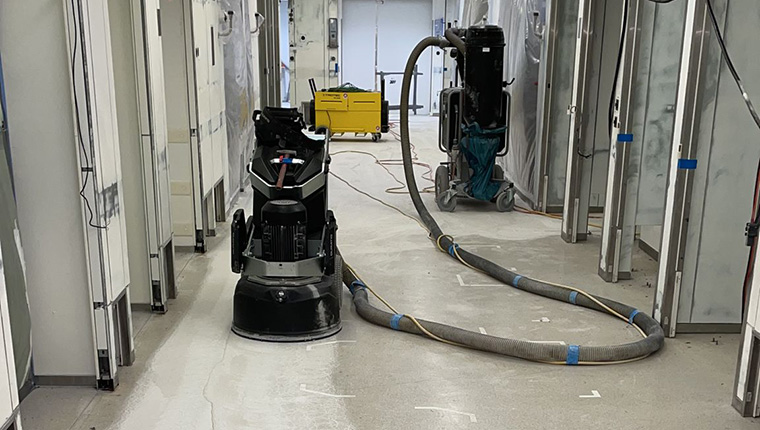
Heat Resistance
Clean rooms in washing areas must be extremely heat resistant since WFI (Water for Injection) is regularly used for cleaning and often reaches temperatures of up to +80°C. However, a standard Pharmaterrazzo, which is applied in these areas, often only suffices for temperatures of up to +60°C. As the floor is constantly exposed to hot water, it gradually becomes porous and fine cracks appear which can lead to severe structural damage over time. To avoid damage and costly repairs, it is important to call in a professional who can advise and recommend a solution which meets your heat resistance and durability needs.
Hot Water Contaminated Drainage
Drains contaminated by hot water in industrial kitchens must withstand extreme temperatures and large amounts of water as they are continuously exposed to hot water from dishwashers, cooking, and cleaning. To avoid distortion and damage, the drains are mostly made of robust, heat-resistant materials, such as stainless steel or special types of plastic. They have been designed to drain off large amounts of water fast and efficiently to prevent flooding or stagnant water. A professional installation and regular maintenance is essential to ensure the drains function well and remain durable.
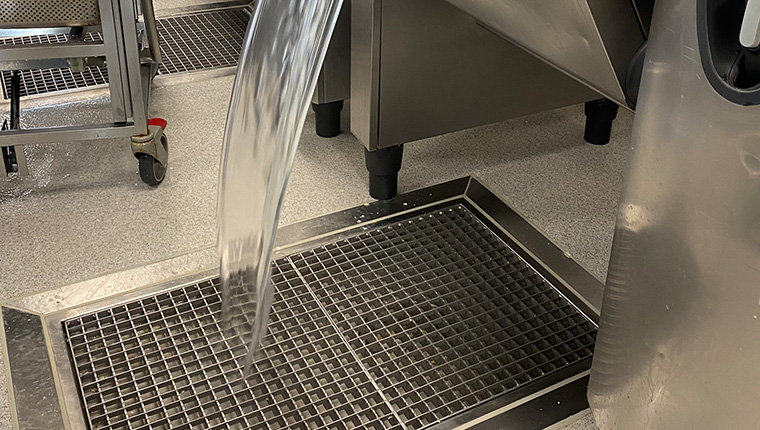
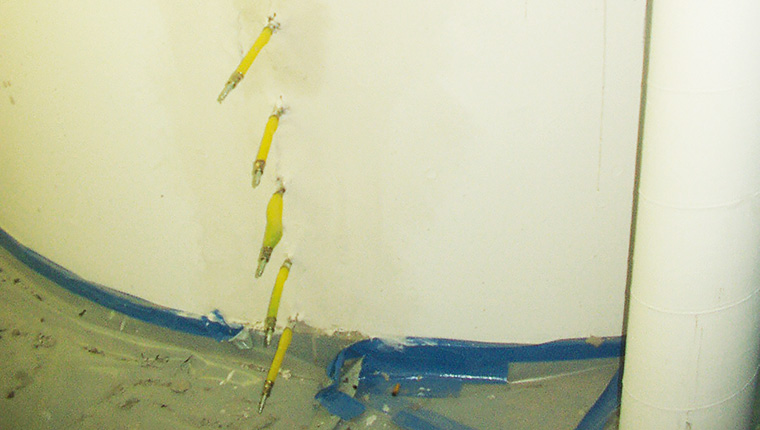
Injection Grouting
Injection grouting is a proven procedure in which materials in liquid form, such as artificial resin, cement suspension, or special gels are injected into cracks, joints, or coves to seal and stabilize building structures. These materials fill the cove entirely and cure after a short time, thereby reinforcing the structure and reliably preventing the penetration of water or other hazardous substances. This procedure is often used to renovate concrete structures and tunnels and to seal cellar walls as it is an effective and lasting solution that upholds structural integrity.
Küchenterrazzo
Our ABC KüchenTERRAZZO® is a robust floor coating which has been especially developed for use in industrial kitchens. This type of coating consists of a two-component reactive resin mix with specially coated quartz sand which is entrenched in a robust, seamless surface. The surface is extremely resistant to moisture, high temperatures, and chemical detergents, making it ideal for intensive use in industrial kitchens. ABC KüchenTERRAZZO® comes in many different colours and designs and is both attractive and functional. Care and maintenance are relatively easy as the surface has no joints or seams where dirt can accumulate.
Material
The choice of material for a clean room depends on various key factors. The most important of which are the specific purpose of the floor, official regulations, and requirements, GMP compliance as well as time schedules for renovations. Other aspects such as chemical resistance, cleanability, robustness, and slip resistance must all be considered. All of these parameters must be carefully assessed to determine the optimal solution to meet your clean room needs and comply with regulations. Sound planning which takes all of these aspects into account is essential to ensure the project can be completed successfully and guarantee long-term operational safety.
Milling
Milling is a crucial process when preparing floor coatings, particularly on concrete or tiled floors. During this process, the surface is sanded to remove old coating and grime and ensure that the substrate is optimally prepared for the new coating This process guarantees an even application and lasting adhesion of the coating. After milling, it is important to ensure that the surface is free of dust and dirt so that the primer or coating can be applied.This is particularly important on industrial floors as the coating needs to be resilient and withstand heavy-duty traffic.
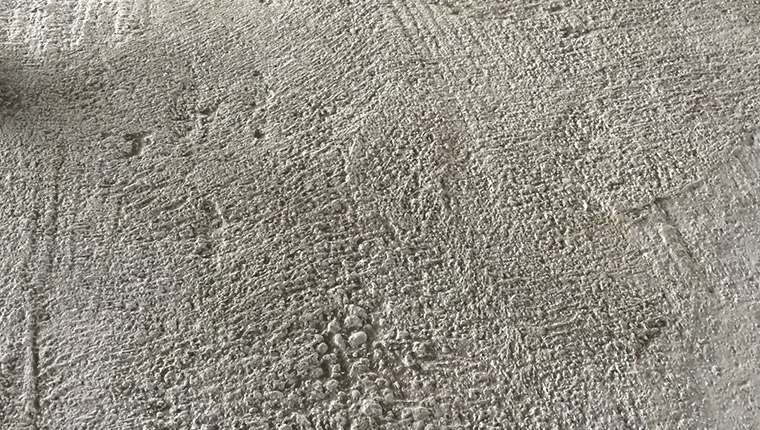
Optical Design
The optical design of cleanroom floors often plays a far bigger role than the aesthetic appeal alone – it is a deciding factor for the functionality and the safety concept of the entire clean room. During audits, the visual quality of the floor is often the first impression that an auditor will gain. A clean and maintained floor immediately demonstrates a high level of production safety. An immaculate floor gives the impression that processes are optimally controlled and this can have a positive effect on the audit result. Not only that, an attractive workplace contributes to employee satisfaction and performance. They feel more at one with their work surroundings and handle the equipment and stocks with more care. Finally, a visually appealing clean room usually reflects high functionality – if a floor is well-cared for, then you can assume that conditions in production are just as excellent.
PharmaTerrazzo
PharmaTerrazzo is one of the most popular floors in clean room and pharmaceutical areas. It convinces with its attractive design and robust features which is why we often recommend it. This floor is not only easy to maintain but also withstands many demands in controlled environments such as clean rooms. However, even PharmaTerrazzo reaches its limits in certain conditions. For example, it is not always the optimal solution for rooms with extremely high chemical or thermal exposure. An in-depth consultation and careful consideration of all your needs and conditions are essential when it comes to choosing the right floor coating.
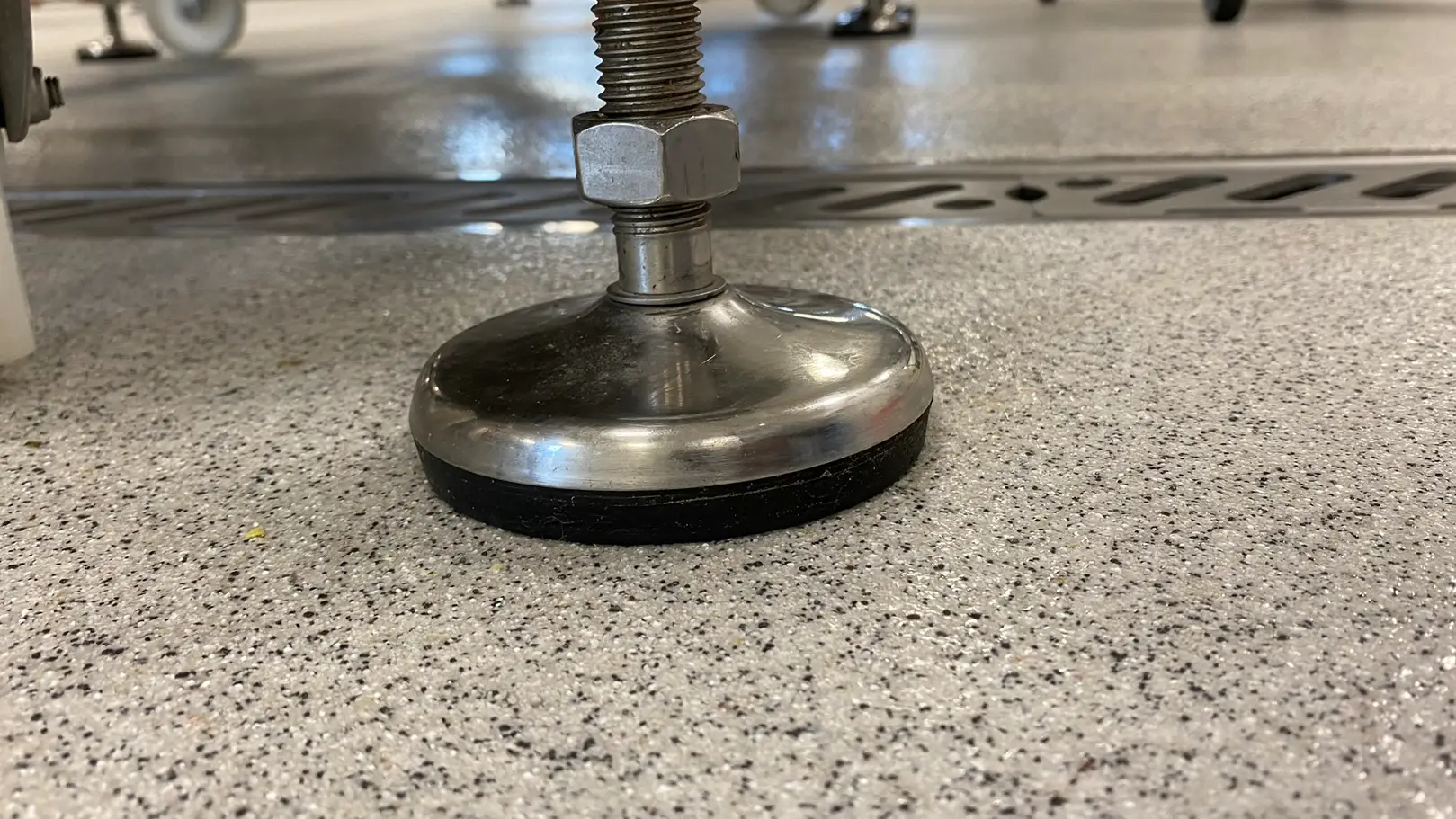
Plasticizer Resistance
Plasticizer resistance is a decisive factor in industrial flooring to avoid damage caused by rubber objects such as machine pads, conveyor belts, or mats. Such rubber objects often contain plasticizer which can lead to outgassing and corrode the floor surface. This often entails discolouring, softening, or even degradation of the coating. Especially in environments where such objects constantly impact the floor, it is important to choose coating which is highly resistant to plasticizers. You can also protect the floor and contribute towards its longevity and aesthetic appeal, as well as prevent costly repairs or replacements, by applying additional sealing or using special underlays
Quality
Clean room quality features are primarily an extremely smooth, seamless surface which is easy to clean and prevents particle accumulation. Furthermore, it must be chemical resistant to withstand aggressive detergents and disinfectants in clean rooms. High abrasion impact ensures that the floor maintains its stability even after intensive use and frequent cleaning. Just as important is its ESD capacity to protect sensitive electronic devices from discharge. Clean room floors must also be low-emission to ensure good air quality and be absolutely waterproof, especially in areas in which liquids are used.
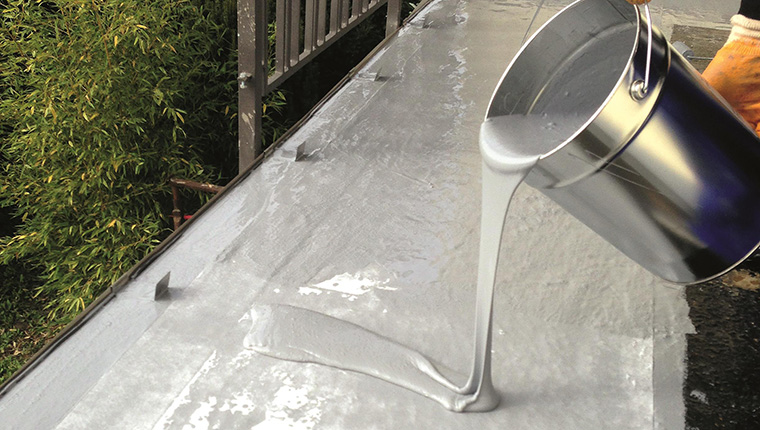
Sealing
Sealing protects buildings from the penetration of moisture, liquids, and harmful substances, thus preventing cracks and spalling. At the same time it significantly prolongs the longevity of the floor. Particularly in wet or chemical environments, high-quality sealing is indispensable. EU regulations stipulate clear requirements and quality standards to guarantee the reliability and safety of the sealing in various areas of application.
Screed/High-Performance Screed
Screed prices for clean room floors fluctuate greatly between €30/m² und €500/m², depending on the type of screed and its purpose. Screed made of Portland cement is the least expensive, but it is also the least robust option as it can distort during the curing process. For this reason it is unsuitable for projects with high-precision requirements. Aluminate cement screed or mixtures are a better alternative: they cure faster, do not distort and are ideal for challenging building projects. Artificial resin screeds convince with extremely short curing times and high solidity and are a particularly recommended choice for clean rooms and conversions during shutdowns. The screed can be applied in the morning and the floor can be ready for use in the evening – ideal for projects with tight schedules and high demands.
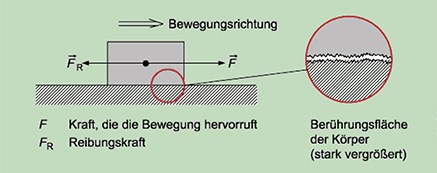
Sliding Friction Co-Efficient
Sliding friction coefficient µ represents the ratio of the horizontal frictional force and the vertical applied force that occurs during movement between a slider and a horizontally accessible surface at a constant speed. This coefficent indicates how much force is needed to maintain movement on a specific surface. It is a deciding factor for the slip resistance of floor coatings. The relevant standards to determine and assess the coefficient are defined in the Austrian ÖNORM Z 1261 for accessible surfaces which ensures that the safety of surfaces, especially in public and industrial areas, complies with all stipulated requirements.
Slip Resistance
The smoother the floor, the easier and cheaper it is to clean. However, the disadvantage is that it increases the risk of slip-related accidents. According to trade association specifications for “Floors in workrooms and areas with a risk of slipping”, rooms must be sufficiently anti-slip with enough displacement space to prevent the risk of aquaplaning caused by liquids. The required slip resistance is stipulated in your building permission. In addition, suitable footwear can contribute towards reducing the slip resistance requirements.
Standards
Standards are essential in clean rooms to ensure that all building requirements are met. GMP guidelines, but also national and international building standards, must be observed. These include a number of aspects, among others the static for the structural integrity of the building as well as sealing regulations to protect against moisture and contamination. Compliance with these standards is key to ensure that clean rooms are suitable for long-term clean room processes. Both the specific industry requirements and general building regulations must be taken into account to meet the standards required for clean rooms.
Stud Structure
Studded floors combine aesthetics and functional benefits. They enhance slip resistance and grip which is crucial in wet or industrial environments. The raised studs enable water to run off effectively, thus preventing puddles from forming and allowing floors to dry faster. In addition, the structured surface gives the floor an interesting texture and optical depth which greatly enhances the overall design of the room. Studded floors are an ideal choice for heavy-duty areas with frequent foot traffic or for outdoor use where weather conditions can greatly impact floor coatings.
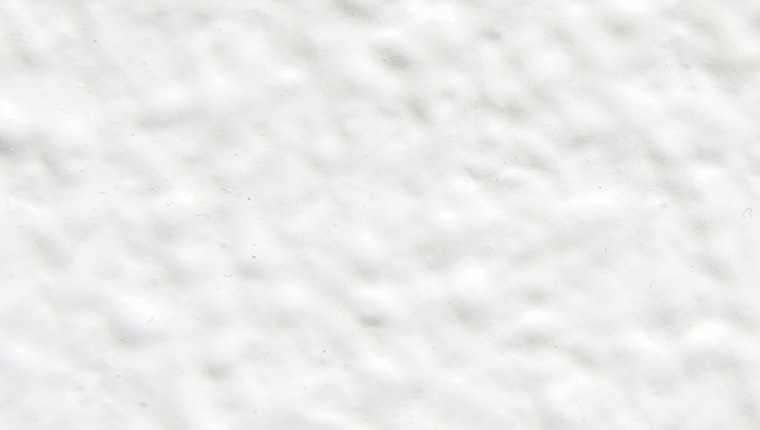
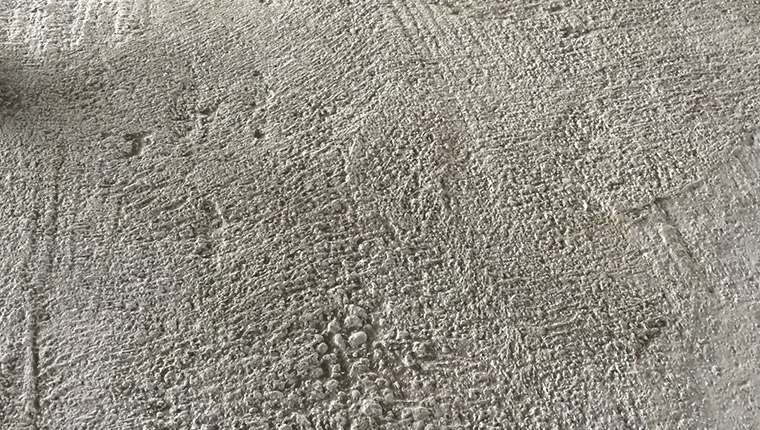
Substrate Inspection
Before applying reactive resin flooring, it is advisable to first inspect the substrate. A careful analysis is the basic requirement when determining the optimal floor construction. This is done by the company that has been commissioned to install the flooring. In this case the adhesive strength and pressure resistance of the screed or concrete is inspected. The surface must have a value of at least 1,5 N/mm². The company will also check that the flatness is in accordance with DIN 18202. The slope formation also plays a role here. If liquid has to be drained, then the slope formation is also an important factor. The substrate will also be checked for damage, such as cracks or damp.
Substrate Preparation
Before flooring can be applied, the substrate is first milled to remove any unevenness and old coating. This is followed by shot blasting, during which shot media are propelled at high velocity onto the surface to clean and roughen it so that the adhesion bonds with the new coating. The next step is grinding to remove even the slightest unevenness to increase the porosity of the floor for optimal floor absorption. This multi-stage process ensures that the substrate remains clean, even, and sufficiently rough to enable permanent, even coating. Finally, the floor is cleaned thoroughly to remove any residue before applying the coating.
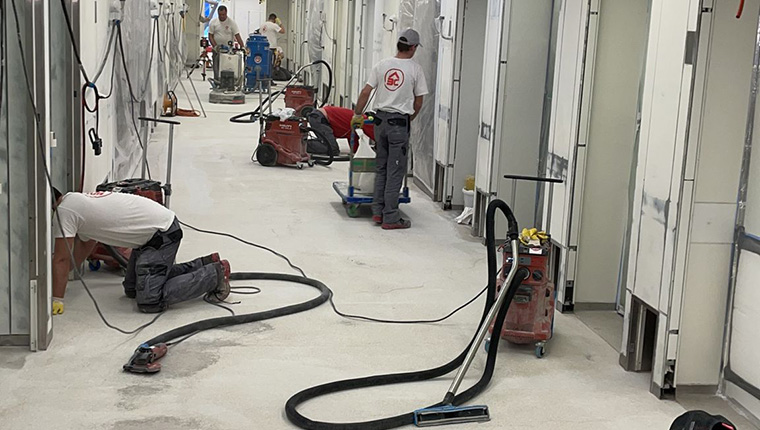
Thermal Expansion in Building Materials
Thermal expansion in building materials occurs when they expand due to a change in temperature or mechanical loads. This expansion is caused by the movement of atoms within the materials, which move more in warm temperatures and increase the distances between them. In order to reduce expansion and its associated material distortion in clean rooms with cooling systems, it is important to take into account the choice of material and how it reacts under controlled temperatures. Fluctuating temperatures can induce stresses which can impact the structural integrity.
Tiles
Before coating can be applied to tiles, the tiled surface must be cleaned thoroughly to permanently remove dirt, grease, and old sealing. Only then can the new coating bond. After this, a primer is applied which improves the bond between the tiles and the coating and supports the durability of the coating. As soon as the primer has dried, the actual coating, usually epoxy or polyurethane resin coating, is applied. These materials are particularly robust and highly resistant to wear and tear. Depending on the product and the desired result, several layers may be needed to guarantee an even, robust and attractive surface. Finally, the coating has to cure properly. It can take several hours or even days before the floor can be exposed to heavy-duty loads, depending on the material.
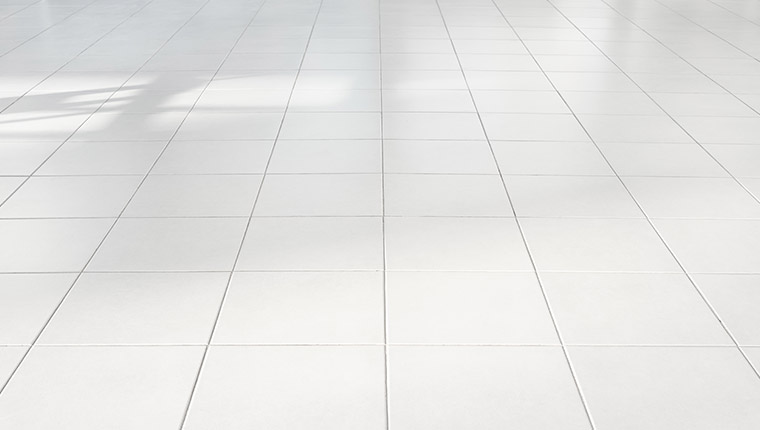
Yellowing
Yellowing on epoxy resin floors occurs when the floor coating turns yellow after long-term exposure to UV rays or chemical reactions. This change in colour is a particularly common phenomenon on floors in areas which are exposed to a lot of sun or intensive artificial lights. While yellowing does impair the optical quality of the floor, it usually does not have any impact on the mechanical properties of the coating. To prevent yellowing or to delay its process, UV-stabilized epoxy resins or an additional protective polyurethane layer can be used. Despite these measures, yellowing is a common occurrence on epoxy resin floors and should be taken into account when planning floor systems.